Table of Content
Kent Modular Home prices range from $70 to $100 per square foot or between $42,000 and $250,000. This price includes delivery, set-up, and utility connections, but excludes total site preparation fees. Kent offers more than 100 customizable floor plans ranging from 600 to 2,500 square feet. Two-story modular homes cost $70,000 to $140,000 on average for the base model and between $105,000 and $210,000 total for all site-work, assembly, and finishing. Most 2-story modular homes are between 1,500 and 2,000 square feet.
In the typical construction loan, the home-buyer often pays for interest that accrues during the home-building process. That expense would be in addition to the buyer’s monthly rent or mortgage payments as they await the home’s completion. Modular homes attached to a permanent foundation are the same or higher-quality than a site-built home, and lasts just as long. Move-in time takes 2 to 6 months, which is 30 to 60 percent faster than site-built homes. Champion retailers can assist with getting permits, preparing the land, installing a foundation, planning utility hook-ups, and all other site work. Champion Modular, Inc. operates under various brands and retailers such as Statewide Homes, Seacoast, and All American Homes.
How Much Does It Cost To Build A Modular Home?
The average modular home costs $50 to $100 per square foot for delivering the base unit, or between $80 and $160 per square foot total with site prep, installation, and finishing. Customized floor plans, designs, and finishes can add $10 to $150 per square foot or more to the total cost. Modular homes can be built on a basement foundation or a pier and beam system with a crawl space. Adding a basement to a modular home costs $20,000 to $29,000 on average, depending on the size. Costs include design, permits, excavation, construction, and finishing costs. Modular log homes cost $50 to $100 per square foot on average, not including site prep, foundation, utility construction, finishings, or assembly, which adds $15 to $80 per square foot.
A 2-bedroom modular home plan costs $55,000 to $90,000, while a 4-bedroom house ranges from $70,000 to $150,000 for just the base unit without set-up, installation, and finishing. Compare modular homes prices and floor plans below to estimate the total cost. The average cost to build a modular home is $80 to $160 per square foot or between $120,000 and $270,000 installed. Setting up a prefab house includes site prep, foundation, delivery, assembly, and utility construction. Modular home prices are $50 to $100 per square foot for the base unit only. Get free estimates from modular home builders near you or view our cost guide below.
Why Choose Brookewood?
When a contract has been signed with Brookewood Builders, we give you a final price. Pre-built homes range in price from $60 to $275 per square foot, depending on the brand, size, floor plan, and customizations selected. A common prefab duplex floor plan is two-stories with 2 bedrooms and 1.5 bathrooms per tenant’s unit, for a total of 4 bedrooms and 4 bathrooms per building. Building a modular duplex may require a custom floorplan and contractors that are experienced in multi-family construction. The average cost of a modular duplex is $100 to $200 per square foot for a complete turn-key installation, depending on the size and customizations required. An average 2,000-square foot duplex costs $200,000 to $350,000 total after site prep, assembly, and finishing.
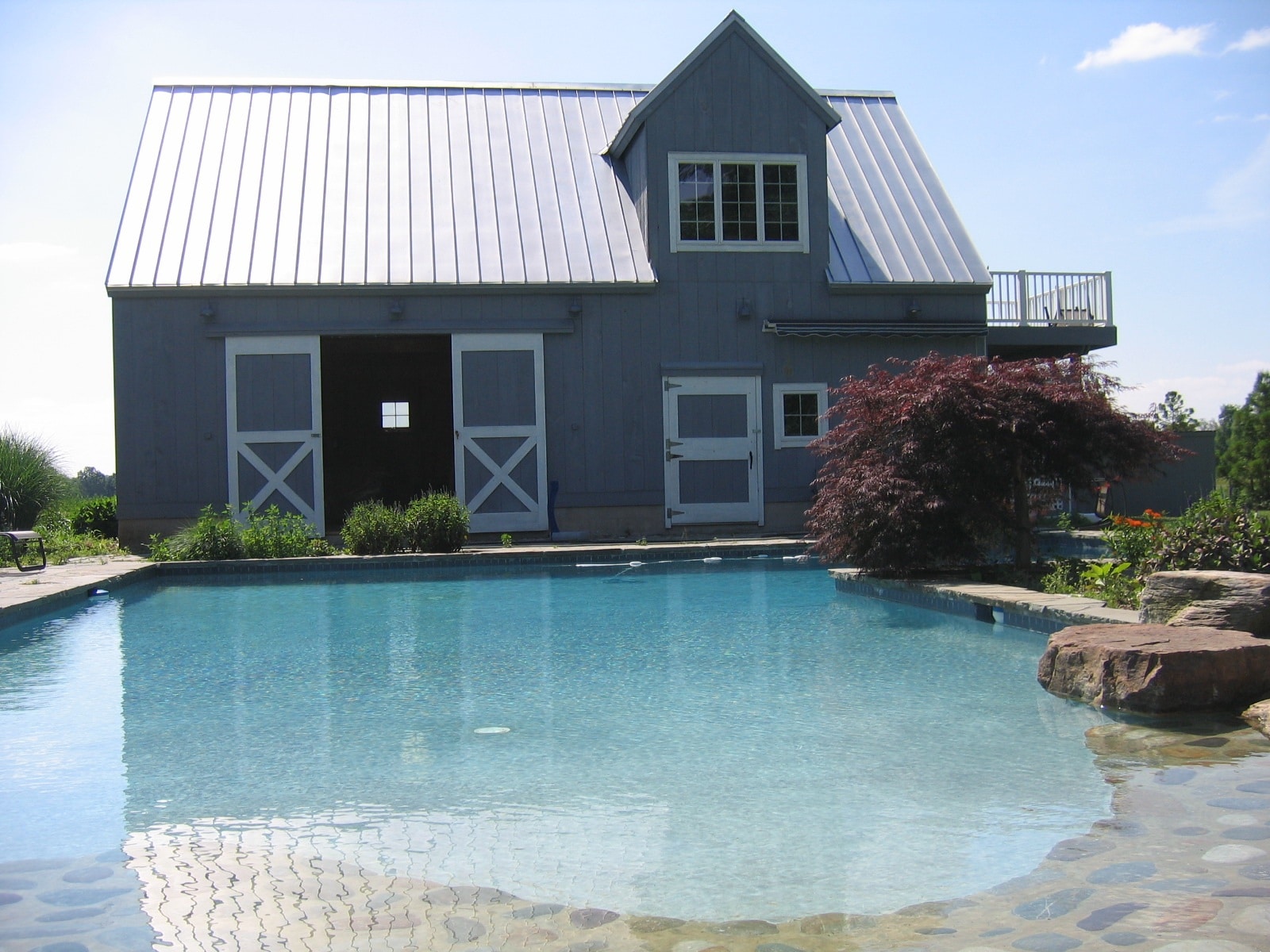
The average cost of building a foundation for a modular home is $6,000 to $20,000 or between $7 and $30 per square foot. Foundation prices depend on the type, location, and size of home. A crawl space starts at $6,000, while building a basement starts at $20,000.
Are Modular Homes A Good Investment?
From foundations to roofing and everything between, we know the importance of each step to insure your project meets exacting standards. We will happily make ourselves available at your convenience to further discuss the possibilities of turnkey financing. With turnkey financing, you have more control over the outcome of the home, so you know your loan isn’t funding a home below your expectations or satisfaction. Before you can be given the keys to your new home, it must pass inspection by numerous parties, including a codes officer, your lender, and yourself. Contractors complete the home finishings and conduct minimal inspections.
You’ll be amazed at just how easy, convenient, and worry free it is to own your new Brookewood Builders home. To get a modular home loan, the top financing options are USDA construction loans, FHA loans, and VA loans that can later be converted to a mortgage. Also, reputable modular home builders will refer you to a recommended lender.
Champion Modular Homes prices range from $90 to $140 per square foot and are typically built and delivered within 2 months. Champion offers over 2,000 pre-designed home plans ranging from 400 to 2,400 square feet that are available nationwide. The average cost to move an off-frame modular home is $5,000 to $15,000 depending on the size, permits, distance, and set-up complexity.
Including lot preparation, financing, and service after the sale. Scot Jalbert was very helpful to him as he made decisions on all aspects of the home, including a custom added porch. Brookewood, and especially Scot, is a contractor that you can rely on to be reasonable, responsive, and accurate. I would not hesitate to use them for a future modular home purchase and installation.
As a Maine Modular Home builder, we specialize in providing a wide variety of custom Modular Home floor plans from trusted Modular Home Dealers. All of our modular homes are customizable from the floor plans to the specified colors. Atlantic Home Solutions is the premier provider of modular homes, mobile homes, and manufactured homes in New England.
Banks tend to offer fewer financing options compared to site-built homes. Modular homes attached to a permanent foundation qualify for more loans, but on-frame modular homes are categorized as mobile homes and may require alternative lending sources. Prefab homes cost $30 to $100 per square foot on average for a base model without the land, finishes, site work, or customizations. Prefabricated houses are cheaper when buying a kit house or shipping-container home.
With the pricing guaranteed, financial institutions realize that cost overruns are eliminated. Dirigo Custom Structures has over 30 years experience building Maine homes. Whether it’s a new deck, custom site built or modular home, we utilize only first class products and suppliers to assure your project meets and exceeds your expectations. The loan begins when you receive the keys to move in, making it a much more affordable and hassle-free process to build a home. We build homes in Maine and New Hampshire known to be the finest quality homes on the market.
Adding a driveway, garage, utility connections, and landscaping are not included in buttoning up. We build to meet or exceed the National Building and Energy Codes ensuring your home is built to the highest standards. Check out a few of our most recent home projects we have completed for our clients. In most instances financing is a necessary part of a new home project and working with the right bank is a key component to the overall project. We pride ourselves on the use of cutting edge building systems as well as old world craftsmanship.
Our experience ranges from bathroom remodels, small backyard decks, additions, custom modular homes, custom site built homes, commercial hotels, and financial institutions. Modern modular and manufactured homes are constructed in climate-controlled building facilities, protecting the construction process and workforce from the elements. This means there’s no worry that Alabama rains or winds will delay construction as they would with a site-built home. Manufacturers employ modern building techniques and the latest construction technologies to build their homes with precision and efficiency. Modular and manufactured homes are built from the inside out—one of the last stages of the construction process is the exterior finish of the home. This enables home builders to better insulate their homes, reducing air leakage and infiltration and resulting in greatly improved energy efficiency.

No comments:
Post a Comment